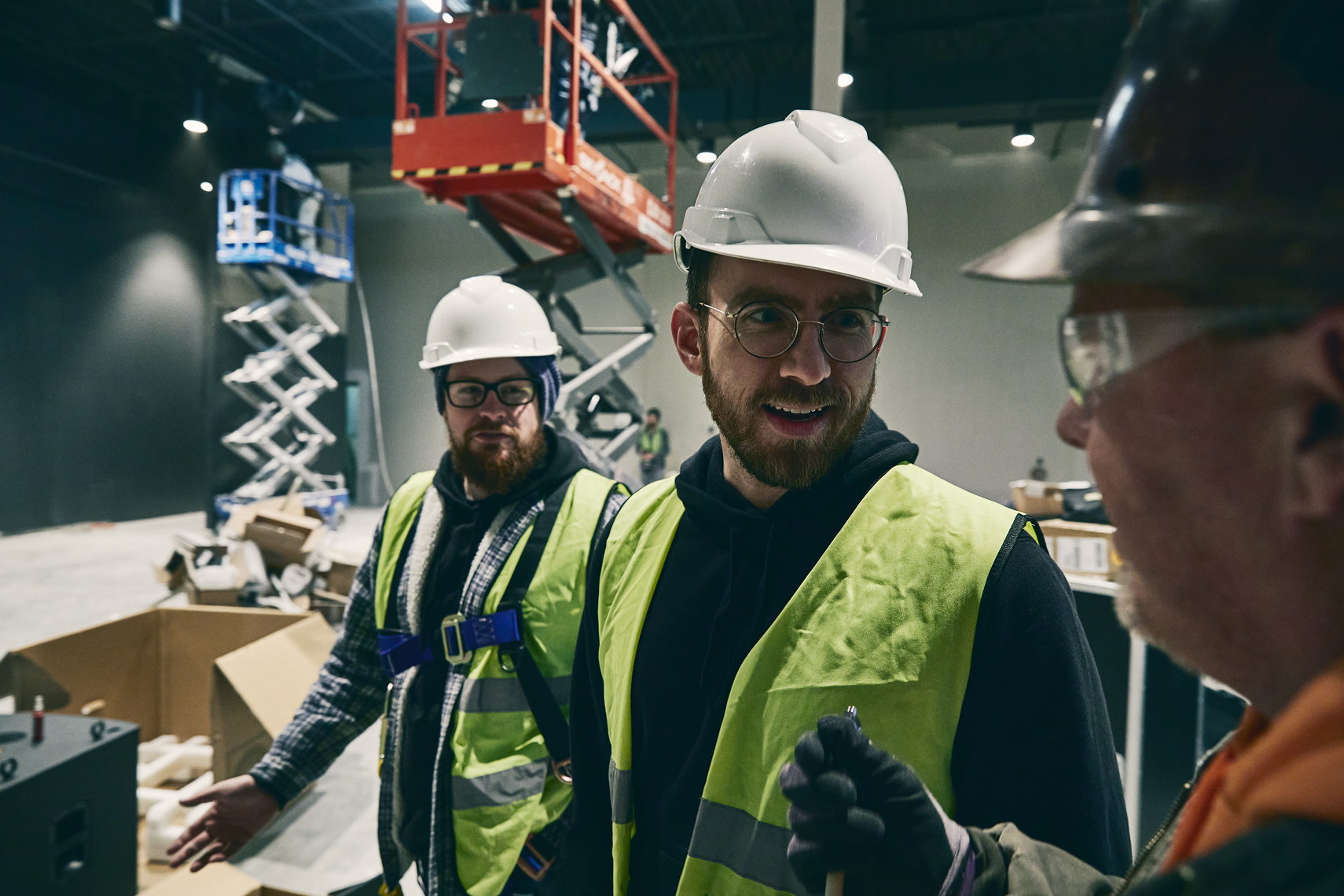
March 14, 2022
A fresh approach to construction projects
Is now the right time to move forward with your construction or renovation project? Or is it fiscally irresponsible in this time of rising construction costs?
With over 60 active projects nationwide in varying design or construction phases, this is a question we face daily. Everyone is asking right now, should we put our plans on hold or move forward despite the circumstances?
Current trends seem to accelerate in challenging times, such as pandemics and recessions. This can be a negative but also may be a catalyst for innovation. We have seen growing success in commercial construction and renovation projects through modular, prefabricated construction methods in the last couple of years. In most cases, this can significantly expedite project delivery at a reduced cost with a higher level of coordination and efficiency.
In new construction scenarios, the interior architectural elements are fabricated while the project is in the structural construction phase. Once the building envelope is dried in and secure, those elements are delivered to the job site and installed, saving significant on-site construction time as multiple scopes of the project are simultaneously accomplished. In most cases, this increases quality and efficiency compared with 100% site-built projects.
The other advantage is accountability. As the fabricator and installer, we are one accountable entity, rather than coordinating and relying on multiple trades and contractors.
Renovation projects also gain an advantage in minimizing major trade work, such as masonry or framing, by covering existing walls with prefabricated panels. The panels can be faux-stone, wood, metal or much-needed acoustic elements with built-in lighting or technology. Tenant infill and retail users are great candidates for utilizing modular walls and interior casework. Office renovations can be driven by a need to update, or more recently coming out of the pandemic, some redesign of open office environments for more personal space without going into construction mode for three months.
After countless projects over 22 years, we’ve proven this modular construction model allows the prefabricator, as one contractor off-site, to take the place of multiple contractors on-site. The fabrication process can employ welders, framers, carpenters, cabinetmakers, faux-finishers and even electricians, as lighting and other technology is integrated into some elements while still in the shop. After being built in the shop, it’s assembled, tested, disassembled, wrapped and shipped to the job site for installation. The end result is renovated spaces in a fraction of the time to that of general construction methods.
Here are some recent examples:
- On a tenant infill project for a bank, a four-month construction schedule was turned into an income-earning tool in two weeks for significantly less cost than a general contractor had estimated.
- In partnership with Ozark-based Torgerson Design Partners LLC, we created a themed environment for CoxHealth in its new pediatric facility. We started with a white box (infill space finished to the level of sheetrock) and turned it into a place for children to feel comfortable, entertained and engaged with a real-life treehouse environment. While the general contractor was doing its work, our crew was fabricating the elements installed in just a few weeks, expediting the project delivery.
- In a project with a 150-seat church, we went from a typical 1960s-looking sanctuary and transformed it into a modern space in seven days, updating the room for under $150,000 without displacing the congregation for a single Sunday service. This renovation was estimated by a general contractor using typical methods at over $250,000 with a few months of on-site work.
- Another project for a downtown Springfield marketing company involved the unique challenge of enclosed office workspaces without permanent wall, floor or ceiling connections. We built modular, branded offices with custom workstations, tables and sit-stand desks. All of these elements went through a standard 3-foot door. Our team installed the infill in one week for less than $60,000, and the client owns it, not the landlord. It can all be moved to another location later.
From my experience, this approach is a win on many levels, not just the end-users. Architects get closer to seeing their actual vision come to life as the fabrication process is a more controlled environment, and they don’t experience vision loss as it moves through multiple disciplines. General contractors can save time and money with one contractor instead of numerous trades to complete a room.
We believe that modular construction is the way of the future as it’s a solution that changes the game – whether it’s a $30,000 or $3 million project.
By Donnie Brawner, Partner Colligo Holdings
CEO, Paragon 360 & Paragon Fabrication
Originally featured in the Springfield Business Journal